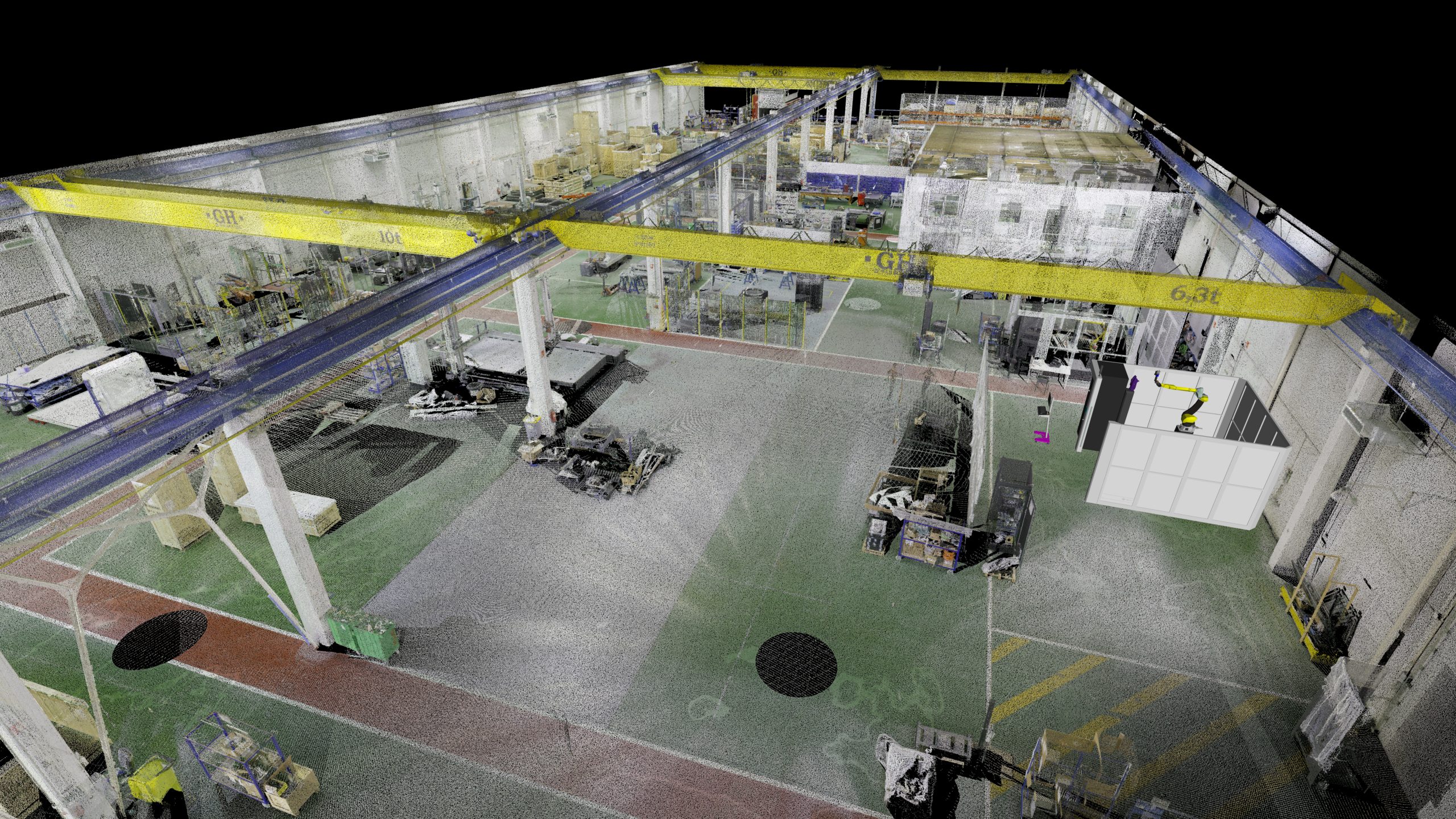
La division Manufacturing Intelligence d’Hexagon dévoile Digital Factory, sa nouvelle solution de numérisation permettant aux fabricants d’établir des répliques numériques très précises de leurs usines. Celle-ci leur permet d’optimiser leurs installations, d’adapter rapidement leurs chaînes de production et d’exploiter des usines plus intelligentes et plus durables. De telles solutions permettraient à un acteur industriel mondial d’économiser une quarantaine de millions d’euros par an* en évitant des erreurs coûteuses et en réduisant de 50 % les frais de déplacement et la formation sur site.
Grâce à ses hautes compétences dans le domaine des équipements de capture de la réalité et de topographie de haute précision, des logiciels pour visualiser, explorer et simuler des scénarios en 3D ainsi qu’un workflow collaboratif performant et intégré au cloud, Hexagon dispose des meilleurs atouts pour traiter ce problème. Les technologies de numérisation sont éprouvées et interviennent depuis plus de vingt ans dans les infrastructures civiles, l’architecture et la sécurité publique. Leur potentiel n’est cependant pas encore pleinement exploité dans le domaine de la fabrication, où des dynamiques importantes obligent désormais les fabricants, en particulier les gestionnaires d’anciens sites industriels, à redéfinir leurs équipements de fabrication et leur gestion de l’espace.
Selon une étude menée par Forrester pour le compte d’Hexagon, 32 % des fabricants estiment que les processus et flux de travail manuels obsolètes ou inefficaces constituent des obstacles à la productivité et à la collaboration. Digital Factory est une alternative évolutive à la planification industrielle traditionnelle qui permet aux fabricants d’améliorer à la fois la productivité et l’efficacité lors des rénovations, en évitant des erreurs coûteuses. Elle optimise aussi la collaboration entre les équipes de fabrication et d’exploitation partout dans le monde. Cette solution s’articule autour de l’optimisation de l’accès à des données à jour dans des environnements virtuels immersifs qui reflètent la réalité. Cela élimine un obstacle majeur à la mise en place d’usines intelligentes aujourd’hui.
Digital Factory exploite un portefeuille complet de solutions matérielles et logicielles qui comprend la gamme primée de technologies de capture de la réalité d’Hexagon – notamment le scanner laser avec imagerie mobile Leica BLK2GO, le module de numérisation 3D autonome Leica BLK ARC pour les systèmes robotisés, et les scanners laser terrestres comme le Leica RTC360 – permettant aux fabricants de capturer et de créer des nuages de points dimensionnellement précis de l’atelier de fabrication. En utilisant la gamme de logiciels Leica Cyclone et Reality Cloud Studio d’Hexagon, basée sur HxDR, les industriels peuvent facilement collaborer et traiter rapidement les données d’Hexagon ou du matériel de numérisation préféré d’un client pour recréer d’une manière rapide et flexible des espaces 3D à jour.
Hexagon propose des flux de travail complets pour maximiser la valeur obtenue par les fabricants dans toutes les phases du processus, de la numérisation de l’usine et du traitement des données en modèles 3D exploitables pour diverses applications jusqu’à la gestion des données dans le cloud. Cette approche permet aux équipes internes et aux sous-traitants d’être plus réactifs et de prendre des décisions éclairées.
Avec Digital Factory, les fabricants peuvent :
- Effectuer des visites virtuelles pour un suivi l’usine – réaliser une visite numérique d’une usine avec un accès à distance, ce qui évite aux responsables et aux sous-traitants de devoir se rendre sur place.
- Collaborer à distance – faciliter la collaboration à distance entre les équipes clés et les parties prenantes à tout moment, en utilisant des outils basés sur le cloud avec des fonctionnalités d’analyse et de modélisation avec accès des données à la demande. Les gestionnaires d’usine et les responsables de production comme l’ensemble de leurs sous-traitants peuvent prendre des décisions à distance et fournir un retour d’information fondé sur des données fiables et à jours.
- Planifier et modéliser des implantations d’usine avec précision et en détail – effectuer un relevé précis d’une usine, pour créer un modèle numérique précis et fiable qui est accessible à tout moment et en tout lieu. Les gestionnaires de sites peuvent surveiller régulièrement, dans les moindres détails, l’avancement de la construction des chaînes de fabrication et éviter ainsi les coûts découlant d’erreurs inattendues.
- Moderniser et installer facilement des équipements – introduire et moderniser des machines telles que les centres d’usinage, les imprimantes 3D, la robotique et les systèmes de métrologie en évaluant leur intégration ou leur remplacement dans un modèle numérique sans risque. Cela contribue à éviter des erreurs coûteuses, par exemple la commande de pièces incorrectes ou un espace insuffisant pour l’installation d’une machine.
- Mettre en place des essais opérationnels et lancer plus vite des nouveautés– en testant de nouvelles machines, des agencements d’usine et des flux de travail dans l’environnement virtuel 3D, les entreprises peuvent rapidement identifier les questions de faisabilité et la considération relative aux émissions, ce qui leur permet de mieux comprendre les avantages potentiels des nouvelles technologies et de rendre possible la vision d’une usine intelligente du futur en une réalité.
« Hexagon a acquis une parfaite compréhension des besoins des fabricants. Digital Factory permet d’intégrer le monde physique dans un espace virtuel précis d’expérimentation industrielle. En collaboration avec leur équipe et leurs fournisseurs, les fabricants peuvent envisager des scénarios hypothétiques pour façonner des conceptions et des agencements d’usine plus efficaces et superviser la mise en œuvre avec des plans 3D irréfutables et accessibles. Nous rendons l’usine numérique plus abordable et plus accessible. Nous sommes ravis de voir comment nos clients mettent en œuvre nos solutions pour optimiser leur activité et rester compétitifs avec des usines plus intelligentes », souligne Benjamin Outrey, Responsable des solutions Digital Factory chez Hexagon.
Le système Digital Factory est conçu pour s’intégrer aux flux de travail existants des clients. Il s’interface avec les applications de modélisation des informations du bâtiment (BIM), les solutions de gestion des actifs d’entreprise HxGN EAM d’Hexagon et les logiciels CAO courants d’AutoCAD et de Bentley.
* * *
*Hexagon estime que le coût de l’absence de réalité numérique d’une usine peut atteindre 210 000 euros par an et par site. Pour une multinationale industrielle avec 200 implantations, cela représente 42 millions d’euros par an. Ce calcul prend en compte les coûts associés aux erreurs dues à des agencements d’usine obsolètes, une réduction de 50 % des frais de déplacement et annexes et un temps de formation sur site divisé par deux grâce à l’exécution de visites et de formations virtuelles. Il tient également compte des économies réalisables en matière de CO2.
La division Manufacturing Intelligence d’Hexagon annonce la nomination de Benoît Coudray en tant que Country Managing Director Sales & Leadership en France. Il répond à Gupta Siddhant, VP EMEA South, Enterprise Accounts & Solutions. Fort de 20 ans d’expérience au sein de la division, Benoît Coudray en orchestrera le développement, au service des entreprises manufacturières, […]
Du lundi 16 au dimanche 22 juin 2025, Hexagon sera présent au Salon International de l’Aéronautique et de l’Espace (SIAE) à Paris Le Bourget. Sur son stand D158 (Hall 2B), le spécialiste de la réalité numérique, présentera une combinaison de suites logicielles et de matériels de précision dédiés au secteur de l’aéronautique. Ceux-ci garantissent une […]
Filiale numérique du groupe La Poste, Docaposte lance une campagne de marque visant à développer la notoriété du leader de la confiance numérique en France et valoriser son image d’entreprise numérique engagée. Déclinant en cinq annonces ses convictions pour un numérique responsable éthique et souverain, la campagne sera déployée en print et en digital à […]